
The compressed crystal produces a charge which is proportional to the pressure.
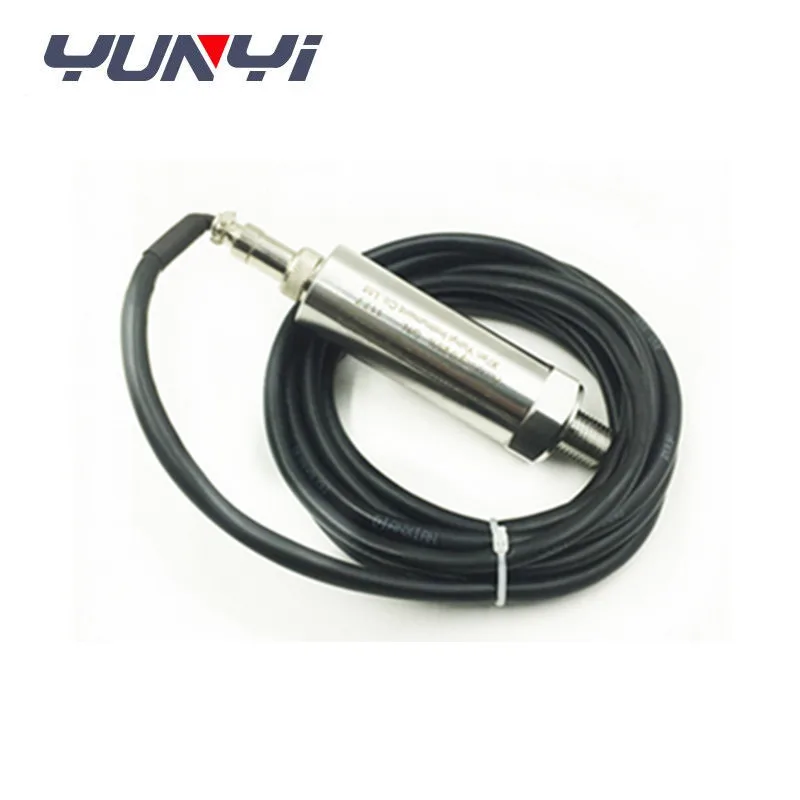
The pressure to be measured acts on the sensor’s diaphragm and compresses the PiezoStar crystal.
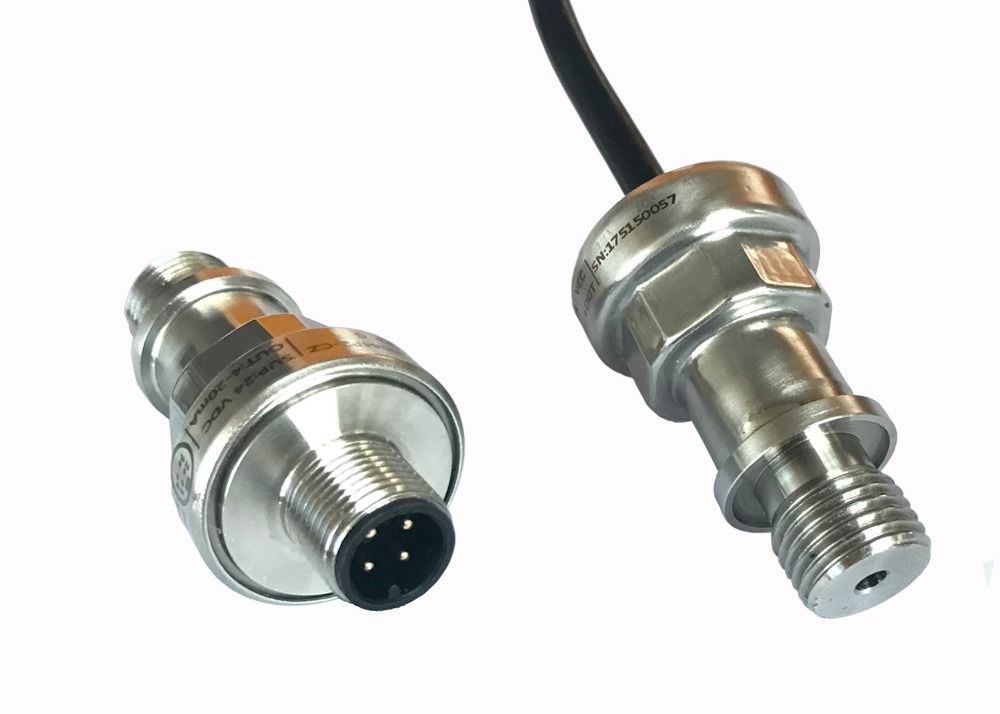
This PiezoStar crystal gives the sensor a far higher sensitivity than an equivalently sized pressure sensor based on synthetic quartz, which results in a lower noise level and so enables lower pressure to be measured more accurately.
Piezo electric pressure sensor series#
At the core of the all-welded, hermetically sealed 601C series there is a high performance PiezoStar crystal grown by Kistler. By contrast, piezoresistive pressure sensors are the right choice when measuring static pressure curves. Another unique characteristic of piezoelectric pressure sensors is their ability to measure small pressure fluctuations that are superimposed on top of high static pressures with exceptional resolution. They have wide uses from medical robotics to acoustics applications.īoth types of sensors can be used for multi-axial applications, and can support compression, shear, or bending stresses.Due to their high natural frequencies, piezoelectric pressure sensors can be used for a variety of applications where dynamic pressures need to be measured. Their small size and excellent dynamic response makes them suitable for highly sensitive applications. Generally, piezoelectric sensor designs are more compact and are more rugged in construction than those of strain gauges. Again, the geometry of the sensor depends on the application requirements. Piezoelectric sensors also include housing designs in these shapes.
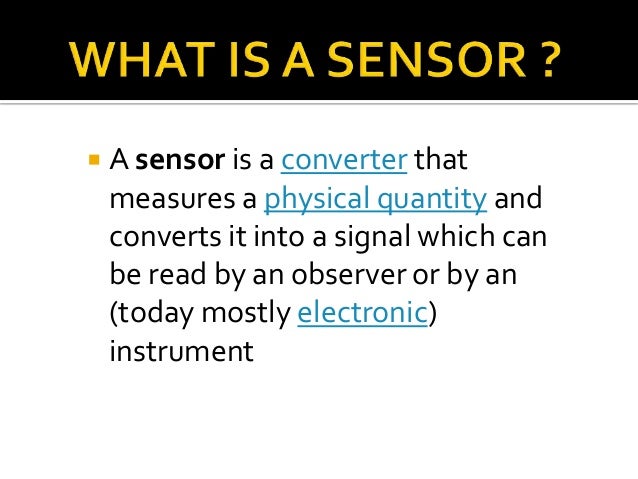
Some examples of so-named load cells are beam, S-shape, disc canister, or planar beam. This diversity allows the load cells to adapt to the needs of different applications.īy convention, the geometric shape of the gauge’s structural housing unit gives the load cell it’s name. The position of the gauge in the structure allows it to capture strains at that location engineers exploit this fact by creating these load cells in different geometric shapes with different load point characteristics. These are durable metal structures that house a strain gauge. Strain gauges most often appear in strain gauge load cells. The bonded strain gauge is preferable as it is more compact and easily embedded in the sensor’s structural element. Note that non-bonded strain gauges also exist, but their use is not as prevalent. The last fabrication step is then to hermetically seal the device to protect it against external mechanical and chemical damages. This involves the steps of cleaning, smoothing, roughening, and marking. Proper bonding requires preparation of the surfaces. The strain gauge is then carefully bonded to the sensor’s structural element surface with adhesives or other bonding agents.
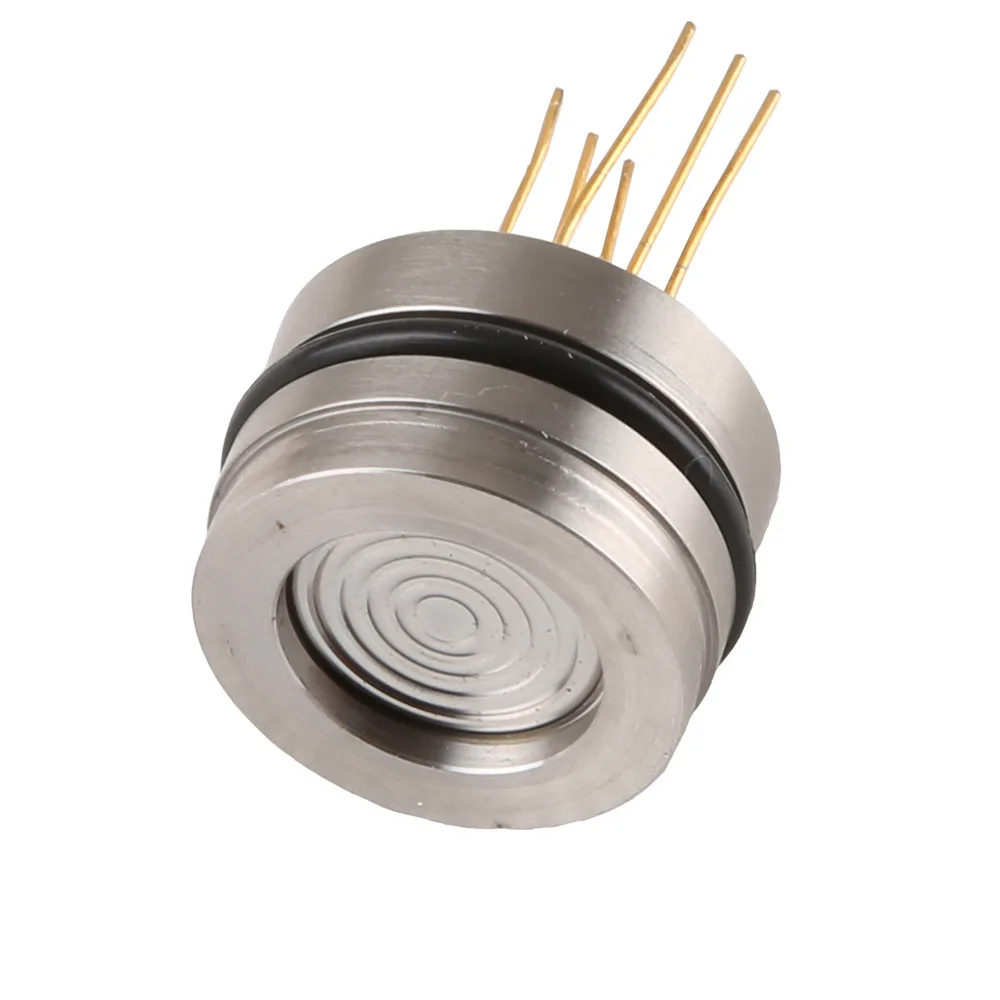
